Understanding Industrial Blower Design: A Comprehensive Guide
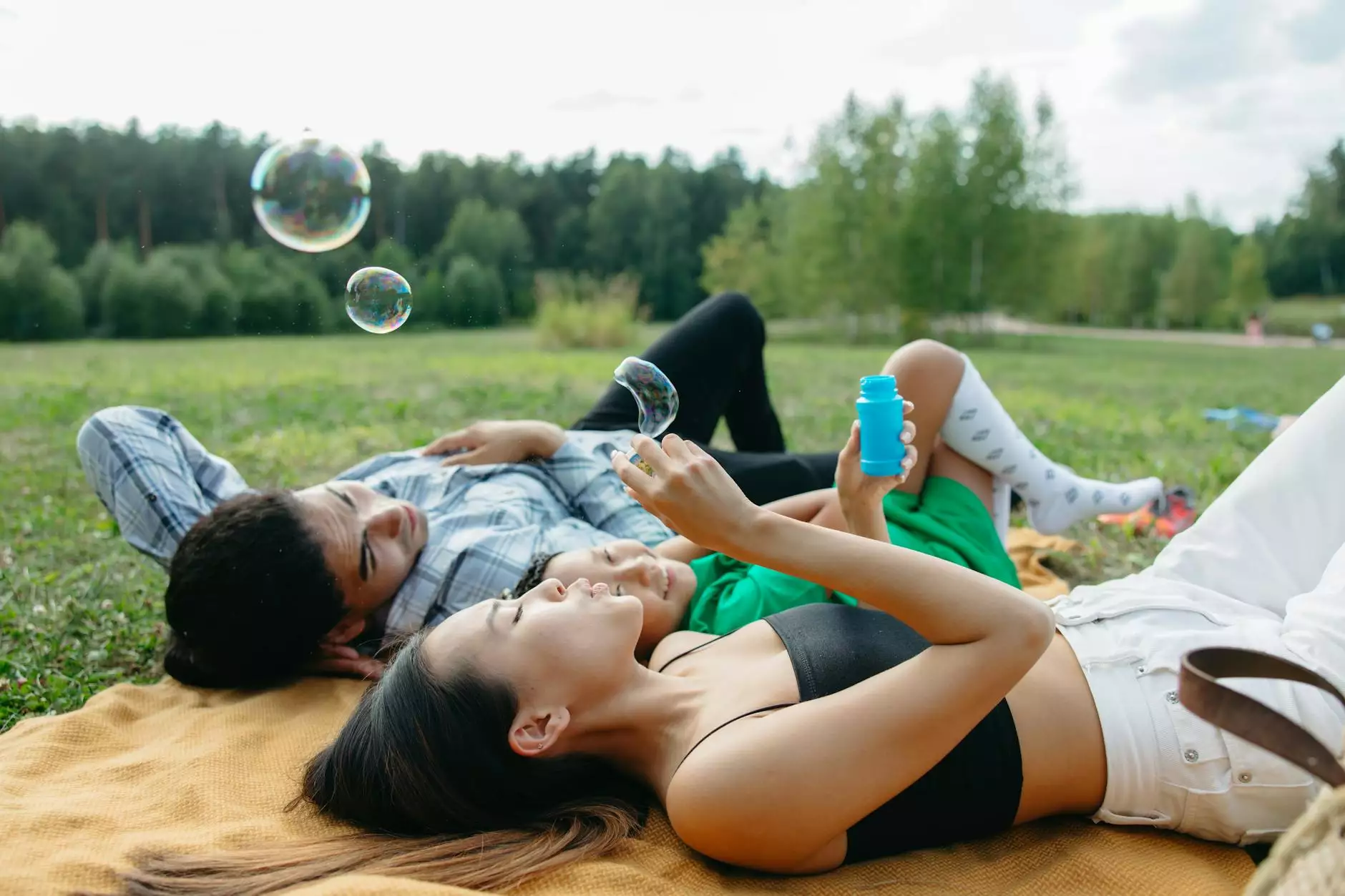
The importance of industrial blower design cannot be overstated in various industrial applications. Whether you are managing a large manufacturing facility or running a smaller operation, understanding the fundamentals of blower design can significantly enhance efficiency and performance.
What is an Industrial Blower?
An industrial blower is a mechanical device designed to move air or gas at a high flow rate. These devices are essential in several applications, including but not limited to:
- Ventilation systems
- Drying processes
- Dust collection systems
- Combustion air supply
- Cooling applications
The Importance of Good Design in Blowers
The design of an industrial blower plays a critical role in its overall efficiency and performance. A well-designed blower can lead to:
- Energy Efficiency: Lower energy consumption leads to reduced operational costs.
- Increased Longevity: A blower designed with high-quality materials and construction will have a longer lifespan.
- Improved Airflow: Optimized airflow can enhance the effectiveness of processes it supports.
- Noise Reduction: Good design often incorporates noise-reduction features for a more pleasant work environment.
Types of Industrial Blowers
Industrial blowers come in various types, each suited for specific applications. Here are some of the main categories:
1. Centrifugal Blowers
Centrifugal blowers use a rotating disk or impeller to generate airflow. They are highly efficient and commonly used in HVAC systems and process industries for air circulation.
2. Positive Displacement Blowers
These blowers move a fixed volume of air per rotation, making them ideal for applications requiring a consistent airflow, such as in pneumatic conveying systems.
3. Axial Flow Blowers
Axial blowers, with their propeller-like design, are suited for moving large volumes of air at lower pressures, making them suitable for ventilation and cooling applications.
Key Factors in Industrial Blower Design
To achieve an exemplary industrial blower design, several critical factors should be taken into consideration:
1. Airflow Requirements
The primary function of a blower is to move air, so determining the required airflow for your specific application is crucial. This involves calculating the volume of air needed and the pressure requirements to ensure optimal performance.
2. Material Selection
Using the right materials can affect not just the durability of a blower but also its efficiency. Materials like stainless steel, aluminum, and composite materials are often selected based on corrosion resistance and weight considerations.
3. Noise Levels
Designing blowers with noise reduction features can significantly enhance the working environment. This involves incorporating sound-absorbing materials and optimizing the impeller design to minimize turbulence.
4. Maintenance Considerations
Designing for easy cleaning and maintenance can prevent downtime and extend the blower’s lifespan. Features such as accessible inspection doors and removable parts are beneficial.
Applications of Industrial Blowers
Understanding the applications of industrial blower design helps you utilize these systems effectively. Here are some of the most common use cases:
1. Wastewater Treatment Plants
In wastewater treatment, blowers are used for aeration. Aeration systems maximize oxygen transfer to facilitate biological processes that break down waste.
2. Pneumatic Conveying
Pneumatic conveying systems transport materials through pipelines using blowers. The design of the blower affects the rate of material transfer and energy consumption.
3. Industrial Drying Systems
In drying applications, blowers help circulate hot air through materials, reducing moisture content efficiently. The design must ensure uniform airflow to prevent hot spots and uneven drying.
4. Material Handling and Dust Collection
Blowers are integral to dust collection systems in factories. An effective design allows for efficient removal of airborne particles, ensuring a clean environment and compliance with safety regulations.
Benefits of Optimizing Blower Design
Investing time and resources into optimizing blower design can yield numerous benefits, including:
- Cost Savings: Improved efficiency often leads to lower energy bills.
- Enhanced Product Quality: Consistent airflow can significantly impact the quality of manufactured products, especially in processes like drying and coating.
- Increased Capacity: A well-designed blower can increase throughput in production operations.
- Environmental Compliance: Better dust and fume control can help ensure compliance with environmental regulations.
Conclusion
Incorporating effective industrial blower design into your business operations is crucial for achieving optimal results. By understanding the different types of blowers, factors influencing their design, and various applications, businesses can make informed decisions that enhance performance and efficiency.
Whether it’s enhancing your Blow Dry/Out Services or optimizing production operations within your facility, the right blower design is pivotal. The investment into understanding and implementing proper design principles will pave the way for improved processes, increased savings, and lowest operational disruptions.
Final Thoughts
When evaluating or designing blowers for your operations, consider collaborating with experts such as TMM located at tmm.com.tr. Their depth of knowledge and experience in industrial blower design can guide you in making the most efficient choices for your business needs.